
What are your company’s goals for the next five years? What tasks are required to reach those goals, and are they represented in your current workflow?ĥ. Think ahead: A workflow analysis is also a good time to ensure that your company is aligning with future goals.Pinpoint weak areas: Look for redundancies, bottlenecks, double data entry and multiple steps that cause delays.Categorize: One way to quickly pinpoint weak areas is to rank tasks based on importance: “vital,” “useful,” “nice but not necessary,” and “should eliminate.” Divide tasks by job description to ensure that the tasks are aligned with the appropriate job title and level of expertise.After you have all the information you need, conduct a workflow analysis, keeping these three steps in mind to help eliminate inefficiencies: During decision points-for approval or denial-what information does the worker need to know in order to make a decision?Ĥ.Are there any deviations from this process?.What activities are involved in each step, and who is involved in them?.What signals the beginning and end of the business process?.This is the requirements gathering phase, where you’ll obtain information from the people involved in each step.ĭuring this phase, ask your employees the following: After you’ve created your initial diagram, you’re ready to dive into the details. Consider this a general overview that shows high-level steps in your process-work or activities that happen repeatedly in your organization.ģ. Next, you’ll want to design a rough sketch of your current business process. Also, are you showing how the process currently works-known as the "as is" process? Or are you showing the “to be” process-how you want the new implementation to look?Ģ. First, determine what point of view you are diagramming for: the business or its customers. There are several steps required to create a successful workflow diagram.ġ. Workflows helped total quality management efforts, as well as Six Sigma-a movement that serves to identify and remove defects in the manufacturing and business process. The 1980s were also a burgeoning time for workflows, as the idea of total quality management became popular and companies aimed to become globally competitive.
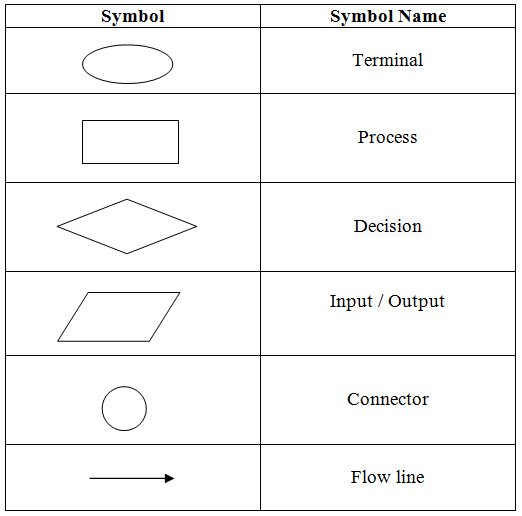
Two major events contributed to the need for rational organization of work: the growing field of optimization theory, and World War II and the Apollo program. As the workplace grew more technologically sophisticated, with the advent of the copier and the typewriter, the ability to further explore and spread knowledge of the workflow system also expanded. The so-called founding fathers of workflows, Frederick Winslow Taylor, a leading proponent of what’s known as scientific management, and mechanical engineer and management consultant Henry Gantt, are credited with being among the first to study the rational organization of labor-particularly in the manufacturing industry. The origins of the modern-day workflow can be traced back to the late 1880s, and the first time the term “workflow” was presented was in a railway engineering journal in 1921.
